Today we discuss Different types of welding tools and their uses. Welding is a versatile and indispensable process used in various industries to join metals together. Whether it’s constructing buildings, fabricating machinery, or repairing structures, welding plays a crucial role in creating strong and durable connections.
Behind every successful welding job are the appropriate tools, each designed for specific tasks and applications. In this blog post, we will explore the different types of welding tools and delve into their uses, highlighting the importance of selecting the right tool for the job.
From electrode holders to welding clamps, protective gear to gas cylinders, each tool has its own unique role in ensuring precise and efficient welds while prioritizing the safety of the welder and the surrounding environment.
21 Different types of welding tools and their uses
- Welding Gloves
- Welding Helmets
- Welding Jackets
- Welding Aprons
- Welding Sleeves
- Welding Goggles
- Welding Respirators
- Welding Curtains
- Welding Blankets
- Weld Magnets
- Welding Clamps
- Welding Pliers
- Welding Wire Brushes
- Welding Chipping Hammers
- Welding Tip Cleaners
- Welding Tip Dip
- Welding Tip Reamers
- Welding Tip Files
- Welding Tip Gauges
- Welding Tip Dressers
- Welding Tip Holders
- Welding Tip Nut Wrenches
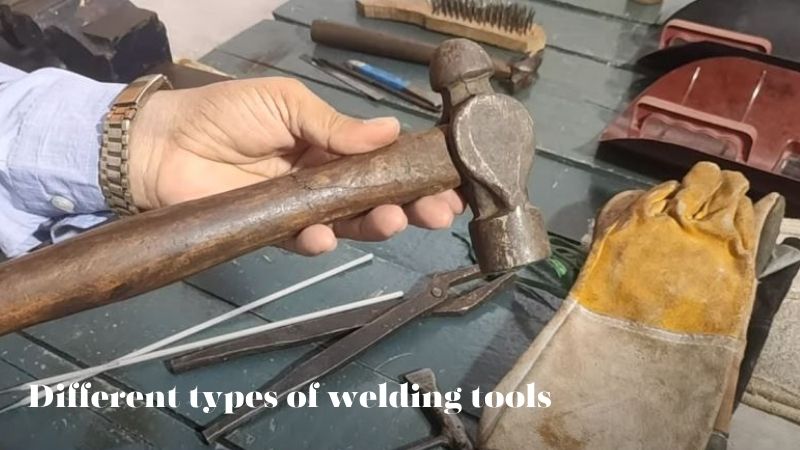
1. Welding Gloves:
Welding gloves serve a crucial purpose in welding operations by protecting the welders’ hands and forearms. The intense heat, sparks, molten metal, and electrical hazards involved in welding. Welding gloves offer high heat resistance, ensuring that the welder’s hands are shielded from burns and heat-related injuries.
The thick and durable construction of welding gloves effectively resists sparks and splatter, providing essential protection. The gloves feature textured surfaces that allow welders to firmly hold and manipulate welding equipment
welding gloves significantly reduce the risk of burns, cuts, and other injuries that can occur during welding operations. They are a fundamental piece of personal protective equipment (PPE) and play a vital role in ensuring the safety and well-being of welders.
2. Welding Helmets:
Welding helmets are the basic protective equipment used by welders during welding. One of the primary functions of a welding helmet is to shield the welder’s eyes from intense ultraviolet (UV) and infrared (IR) light generated during welding.
Welding helmets provide full coverage to the face and head, protecting the welder from sparks, spatter, flying debris, and other hazards present during welding. Welding helmets with appropriate shading filters effectively block out harmful radiation, safeguarding the welder’s vision.
Some welding helmets incorporate respiratory protection features, such as an integrated respirator or a flip-up design that allows the welder to wear a separate respiratory mask. In short, welding helmets are crucial safety equipment for welders, offering essential protection for the eyes, face, head, and respiratory system.
3. Welding Jackets:
Welding produces sparks and spatter that can fly in various directions. welding jackets are designed to be durable and resistant to abrasions and cuts. The jackets also have ergonomic designs that enable welders to move their arms and torso comfortably while maintaining a high level of protection.
Many welding jackets come with multiple pockets and storage options, allowing welders to keep essential tools and equipment close at hand. Some jackets may also have additional features like reinforced seams, high-visibility panels, or reflective strips for enhanced safety.
In short, welding jackets are essential protective clothing for welders, offering vital defense against heat, flames, sparks, UV/IR radiation, and other welding-related hazards. They provide comfort, mobility, and durability while ensuring the welder’s safety and minimizing health risks.
4. Welding Aprons:
Welding aprons serve several important purposes and offer various benefits. Welding aprons cover the front of the body, including the torso and legs, protecting the skin and clothing from burns and other injuries caused by contact with these hazards. It prevents direct contact with hot surfaces, reducing the risk of burns and thermal injuries.
Welding aprons provide coverage to the body, including the arms and legs, shielding the skin from harmful ultraviolet (UV) and infrared (IR) radiation emitted during welding. welding aprons are designed to be comfortable and allow freedom of movement.
In short, Wearing a welding apron is an important safety practice in the welding industry, promoting a safe working environment and safeguarding the well-being of welders.
5. Welding Sleeves:
Welding sleeves shield the arms from sparks, molten metal, and welding spatter generated during welding. They provide a barrier between the skin and these hazards, preventing burns and other injuries.
Welding sleeves help prevent arc flash or welder’s flash, which can cause sunburn-like injuries and long-term damage to the skin. Welders can move their arms comfortably while maintaining a high level of protection. These sleeves are commonly used in metalworking, blacksmithing, woodworking, and other industrial and construction activities where similar hazards may be present.
6. Welding Goggles:
Welding goggles are a safety tool used to protect the eyes during welding operations. They play a crucial role in safeguarding the welder’s vision from the intense light, heat, and potential hazards associated with welding.
Welding produces a bright arc that emits harmful UV and IR radiation. Welding goggles filter blocks the majority of UV and IR radiation emitted by the welding arc, allowing only a safe amount of light to reach the eyes. Welding goggles also act as a barrier against sparks, molten metal, and other debris that are produced during welding.
Different welding processes require different shade numbers. For example, lower shade numbers (e.g., 8-10) are suitable for low-intensity welding, while higher shade numbers (e.g., 12-14) are used for high-intensity welding or cutting processes.
7. Welding Respirators:
Welding respirators protect welders from inhaling hazardous fumes, gases, and particulates. Welding generates various hazardous substances, including metal fumes (such as aluminum, chromium, and manganese)and gases (co, ozone, etc). These can lead to respiratory problems, lung damage, and long-term health issues.
Welding respirators, equipped with appropriate filters, prevent welders from inhaling these fumes and reduce the risk of respiratory elements. This is equipped with HEPA filters, preventing them from the welder’s respiratory system.
8. Welding Curtains:
Welding curtains act as a barrier between the welding area and other sections of the workspace. They help to contain sparks, splatter, and debris generated during welding. This protects individuals from potential burns, eye injuries, and other hazards associated with welding.
Welding curtains are designed to block UV rays and minimize their exposure to workers outside the immediate welding area. The curtains help to shield nearby workers from the harmful effects of the flash. They protect against burns, UV radiation, welding flash, and the spread of fumes or particles.
9. Welding Blankets:
Welding blankets are made of flame-resistant materials that can withstand high temperatures and sparks. They are particularly important when working in close proximity to combustible materials. This protects nearby surfaces, equipment, and personnel from potential heat damage. When welding, small molten metal droplets called spatter can fly off and cause damage or injury. Welding blankets catch these spatters.
Welding blankets can be especially beneficial in cold or windy conditions. It’s also useful after welding to cover and protect newly welded joints, preventing rapid cooling and potential cracks or defects. They can often be reused, providing cost-effective protection over time.
10. Weld Magnets:
Welding magnets are made of strong magnetic materials, such as neodymium or ferrite, and come in various shapes and sizes. this holds metal workpieces in the desired position during the welding.
Weld magnets make it easy for welders to achieve accurate and high-quality welds. They eliminate the need for constant adjustments. It can be used in welding applications, including butt joints, fillet welds, and T-joints. Welding magnets reduce the need for welders to use their hands to steady the materials.
They do not require any complex setup or special skills. welding magnets provide accurate angles, increasing productivity, reducing distortions, and enhancing overall safety.
11. Welding Clamps:
Welding clamps serve several purposes and are of great importance in ensuring the success and quality of a welding project. Welding clamps firmly hold the pieces to be welded in the desired position.
When metal is heated during welding, it tends to expand and contract, potentially causing distortion in the workpiece. This stability enhances the safety of the welder. Welders can focus on the actual welding work instead of having to constantly reposition.
Welding clamps can be used for holding flat plates, pipes, angles, and other irregularly shaped workpieces. When welding multiple parts together to form an assembly, clamps are indispensable for holding all the components.
12. Welding Pliers:
13. Welding Wire Brushes:
14. Welding Chipping Hammers:
15. Welding Tip Cleaners:
16. Welding Tip Dip:
17. Welding Tip Reamers:
18. Welding Tip Files:
19. Welding Tip Gauges:
20. Welding Tip Dressers:
21. Welding Tip Holders:
22. Welding Tip Nut Wrenches:
Safety precautions when using welding tools
No, a laser pointer cannot be used as a welding tool.
Yes, there are specialized welding tools designed specifically for underwater welding.
Yes, there are specialized welding tools specifically designed for working with stainless steel.
No, there are no welding tools that use magnets instead of heat to join metals.
No, a soldering iron cannot be used as a substitute for a welding tool.
Proper safety measures, such as wearing protective gear and working in a well-ventilated area, should always be followed when using welding tools.
No, a microwave oven should not be used to heat metal for welding purposes.
Yes, there are advanced welding tools available that offer automation and precision capabilities.