How to weld exhaust pipe
If you have a welding machine and basic knowledge of how to weld exhaust pipe, you can fix your damaged exhaust pipe by yourself in your garage’s comfort. Fixing your damaged muffler is simple and straightforward. However, you need to have some basic welding knowledge to get the best results. This post will discuss how to weld exhaust pipe with flux core, stick, and mig.
The muffler is one of the most crucial parts of your car. It not only helps to reduce the amount of noise produced by the engine, but it also helps to control the backpressure, thus boosting the performance, fuel efficiency, and endurance of your engine. But just like any other crucial part in your car, the exhaust pipe usually wears down with time and needs repair to keep them in great shape. One common problem that most motorists experience is a broken exhaust pipe.
Different steps and requirements of welding
Before you start welding your exhaust pipe, the first thing you need to do is ensure that you have all the necessary welding equipment. You need to have important welding tools aside from a welding machine, including a circular, saw, hacksaw, grinder, and the right welding gears, including masks, gloves, and welding clothing. Below are the steps to follow when welding your exhaust tube.
Step one: Cut the exhaust tubing
The first and also the most crucial step of this process is cutting the exhaust tubing. How you cut the exhaust tubing will determine the results. You, therefore, need to be careful and cut the exhaust tubing precisely. Start by marking where you want to cut on the tubing, then use a hacksaw or chain pipe cutter to make precise straight cuts.
Please do your best to cut as straight as possible. The only way for the two pieces to merge perfectly is if you make a straight cut. If the cuts are not straight, they may have to purchase new exhaust tubing, which is quite expensive. Once you are done cutting, use a grinder to make the edges finer and remove any defects. Grinding also helps to remove paint, rust, and dirt on the exhaust tube’s surface. This is important as it allows you to get clean, impurity-free welds.
Step two: Clamp the pieces together
Once you have cut the tubing and grind to remove defects, the next process is locking the pieces together before you start welding. Use a C-clamp designed for clamping welding objects to clamp the two pieces together. Before you start welding, make necessary adjustments if necessary, until the two pieces lock together perfectly. Once you start welding, adjusting two pieces will be challenging. Ensure that they have clamped together correctly before you start welding because there is no turning back once you start welding.
Step three: Apply spot weld
Because the exhaust tube is thin, you need first to apply spot welds. Gently apply spot welds 3-4 times around the tubing circumference. The high heat produced from welding will help prevent the exhaust tube from bending. If you notice gaps on the opposite side of the exhaust tube, gently bend it back into place. The spot weld will still hold the locked tubing together, meaning that bending it back into place will not cause any damage.
Step four: Weld the gaps
Once you are done with spot weld, the final step is welding the remaining gaps in the exhaust tube. Weld around the tubing circumference keenly to close all gaps. This process is crucial as it helps the two clamp pieces hold firmly and prevent leaks from developing in the future. It is advised that you weld again on spot welds to strengthen the clamped pieces.
How to weld exhaust pipe with flux core
This is not the best way to weld a damaged exhaust pipe, but it can still deliver great results if performed correctly. Before you start welding using this technique, there are several things you need to do. The first to do is clean the exhaust tube. This will help reduce the amount of spatter produced by the machine. The second important thing to do is to lower the amperage. This is because the flux core welder is likely to produce a hotter arc. Lastly, you need to reduce the wire feed speed. This will help prevent heat from damaging the tubing because of high heat.
pros | cons |
---|---|
It is cheaper than using MIG wires | It produces more spatter |
Welding can be done without using a gas shielding tank | You are more likely to burn through thin metals hence require high precision |
It offers better penetration than when using a solid MIG electrode | |
The cost of this welding equipment is by far cheaper than MIG and TIG welding | |
A wire is fed continuously, meaning that there no need to change the electrode frequently as it is the case with stick welding |
Safety tips for using flux core weld
• Always wear gloves that protect your hands and forearms. Flux core welding produces a very hot arc that can burn your skin.
• Wear long fire-resistant pants to protect your legs against injuries from the parks produced.
• Wear closed shoes to protect your toes from the spark produced by the machine when welding
• Wear goggles to protect your eyes from heat generated and damaging UV from the arc
How to weld exhaust pipe with stick welding
Like flux core welding, stick welding is also not the perfect method for fixing a damaged exhaust pipe. However, if done correctly, this welding technique can deliver excellent results that will amaze you. But this welding technique is not for the faint-hearted. It only works for people who are ready to think hard and come up with a smart solution that will deliver the results they are looking for.
The first thing you need to do when using this welding technique is to determine the right rod to use. We recommend the 6011 rod due to its ability to deliver precise welds on soft surfaces. Select the thinnest 6011 rods that you will find on your local welding store. The 6011 rods will help you in spot welding before you finally weld around the exhaust pipe. Even though stick welding is not affected by dirt, dust, rust, and paint, we recommend that you first clean the tubing to avoid slag that may compromise your weld’s quality.
pros | cons |
---|---|
Stick welding can be done both indoors and outdoors | If the welding process is not done well, stick welding can produce slag that may cause leaks |
Stick welding is not affected by dirt, paint, and rust as it is the case with other types of welding | It uses numerous electrodes. |
It is cost-effective and easy to perform. You don’t need to have specialized skills to weld | |
Stick welding can be performed on all weather conditions |
Safety tips for stick welding
How to MIG weld exhaust pipe
MIG welding is a better technique to weld mufflers compared to stick and flux core welding. This welding technique will not only help you fix your damaged exhaust pipe, but it will make you look new. Before you start welding, prepare the base metal by cleaning the tubing thoroughly to remove paint, dust, and rust. We recommend that you use a metal brush to clean the tubing because it cleans fast and efficiently. { Top-rated Mig welders 2020}
When welding your muffler, we recommend that you combine argon and carbon dioxide. Additionally, the amperage should be adjusted to medium to avoid burning the soft tubing surface.
pros | cons |
---|---|
You can perform your welding using full and semi-automatic methods | It cannot be performed outdoor or in windy conditions |
There flux when welding thus no need of worrying about slag | It requires an external shielding gas tank, thus quite demanding |
It is faster and more efficient welding techniques than stick and core welding | |
MIG welding can be used on alloys because of its versatility |
Safety tips of MIG welding exhaust pipe
• Always wear closed shoes to protect your feet from sparks
• Wear fireproof gloves before welding. MIG welding produces a hot arc that can injure your hands
• Wear a mask to protect yourself against harmful UV rays and deadly fumes.
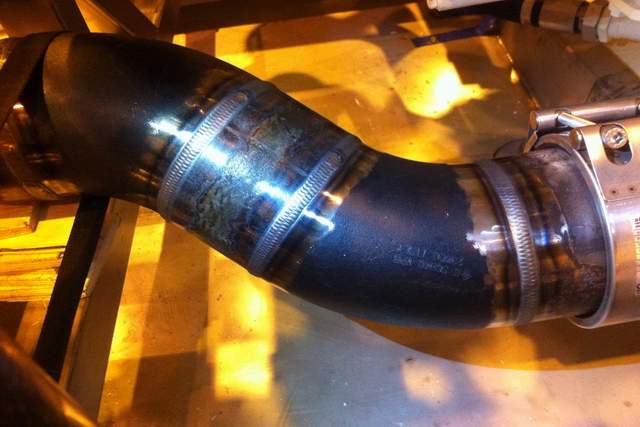
Conclusion
Mufflers are extra sensitive to heat because of the soft material that they are made of. Therefore, it is vital to weld keenly and precisely to prevent welds from running through the base metal. All the welding techniques that we have listed above have their pros and cons. We recommend that you choose a welding technique that you are well conversant with and confident that will give you quality results.
I think, now you better understand the 3 most common techniques of how to weld exhaust pipe systematically.